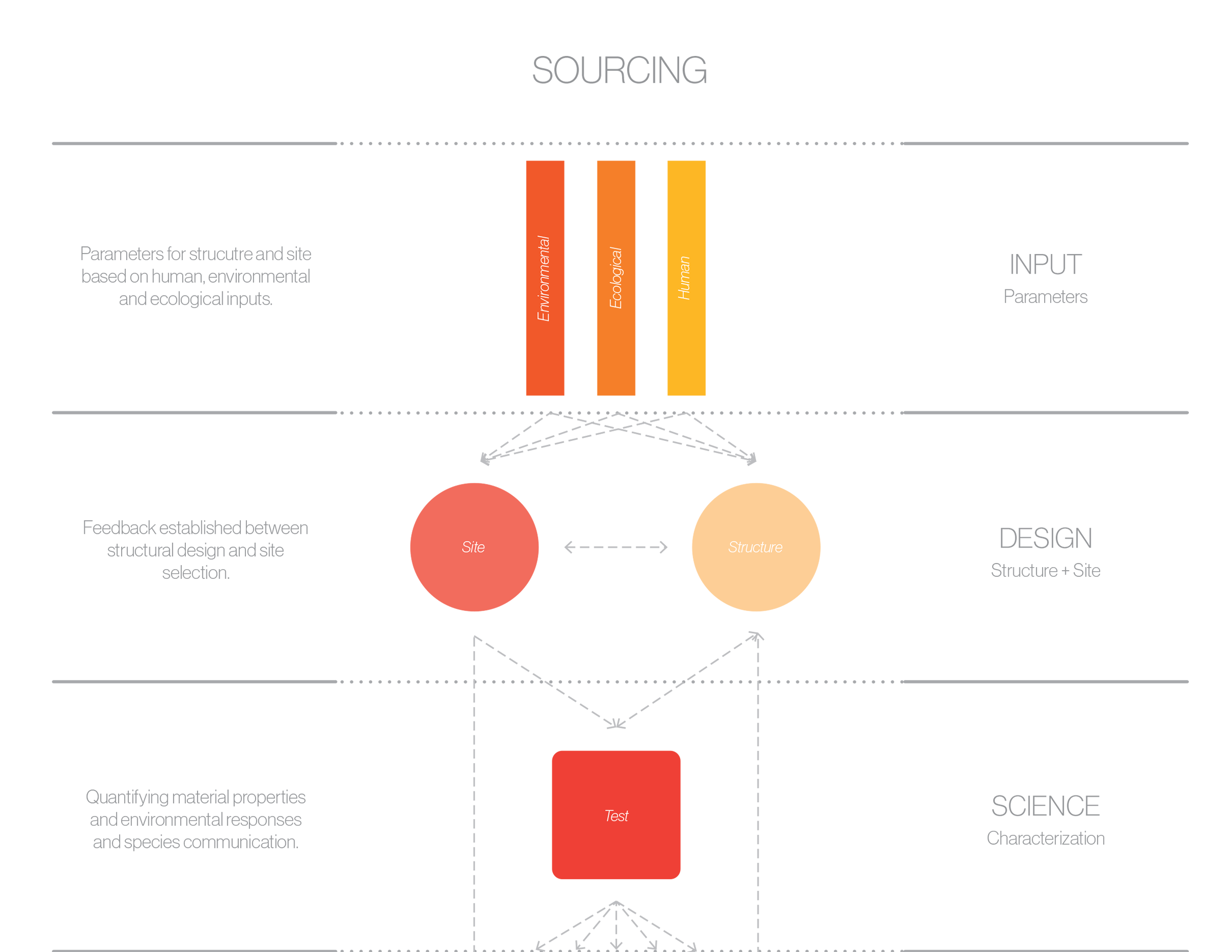
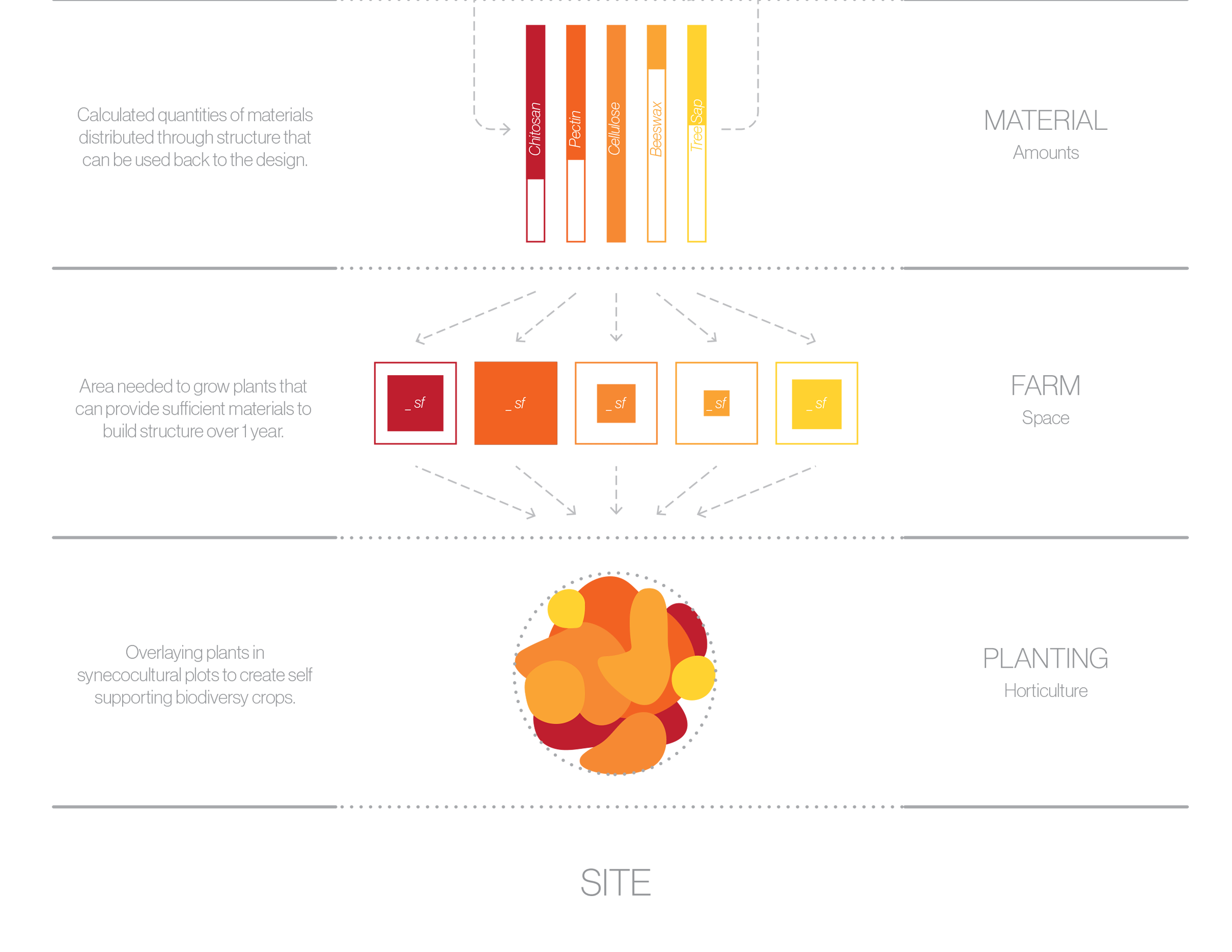

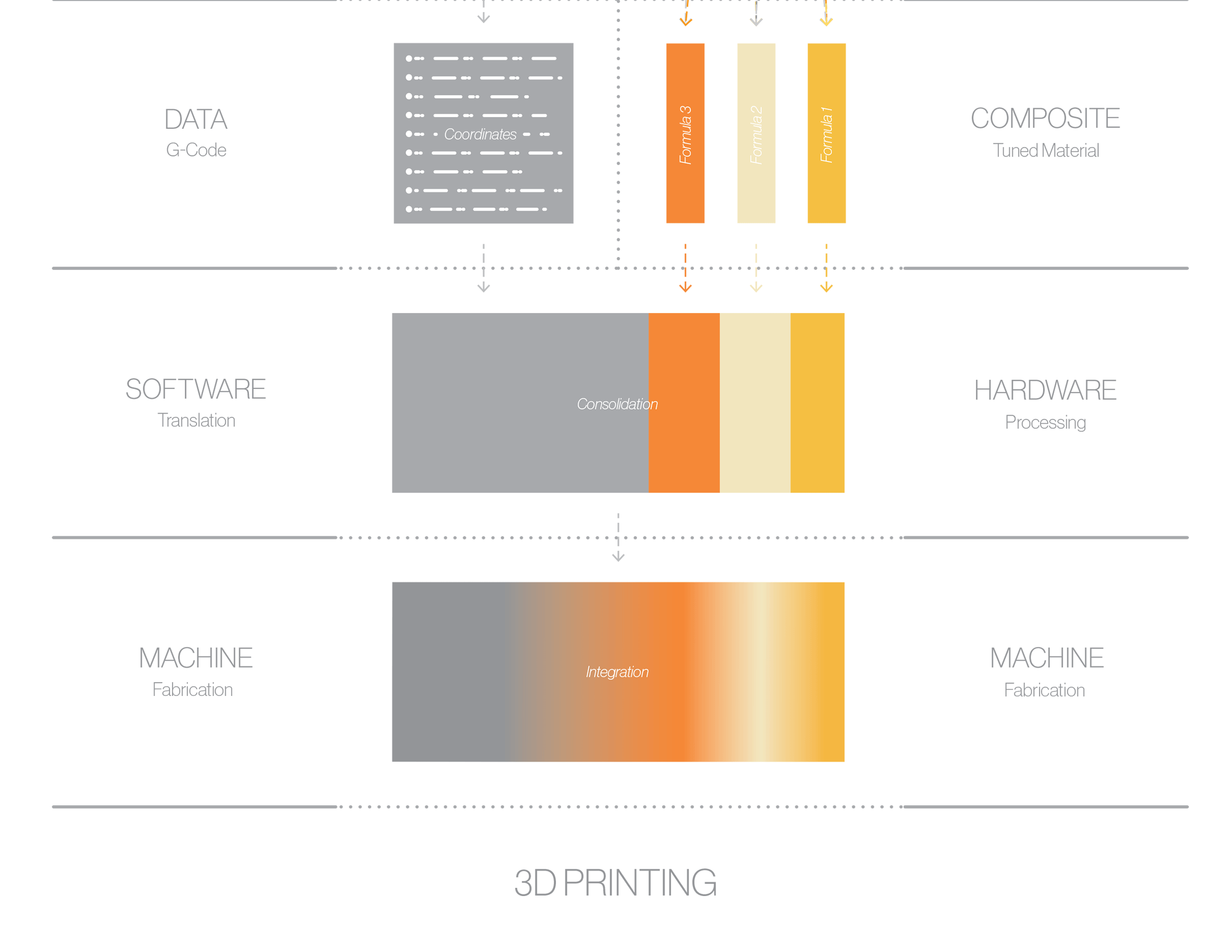
Figure 1: Diagram illustrating the design and implementation process for creating site specific structures from locally grown materials capable of reacting to the climate and organisms in an ecology.
Figure 2:
Diagram presenting the parallel process of transforming digital design parameters and physical material properties into extrudable biopolymer hydrogel 3D prints.
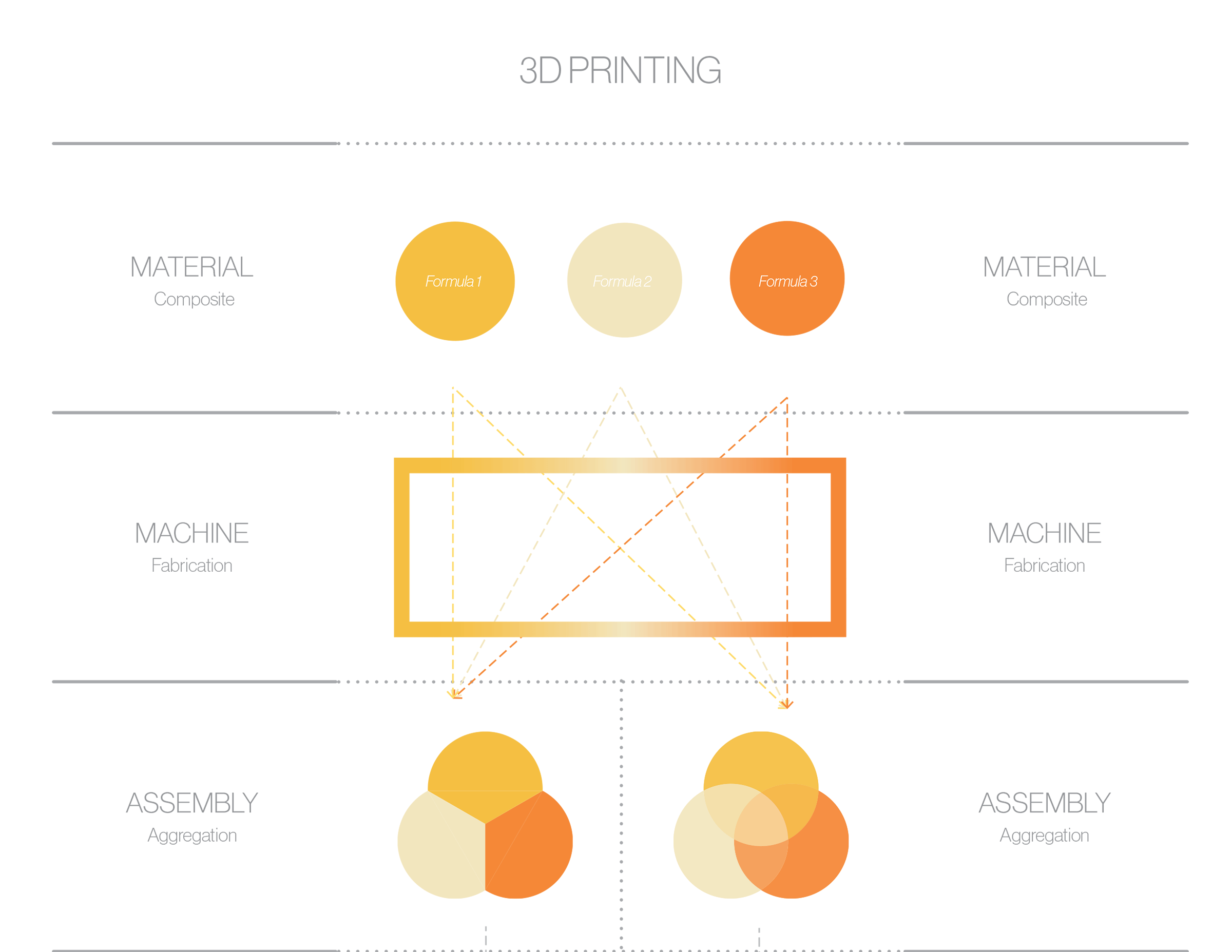
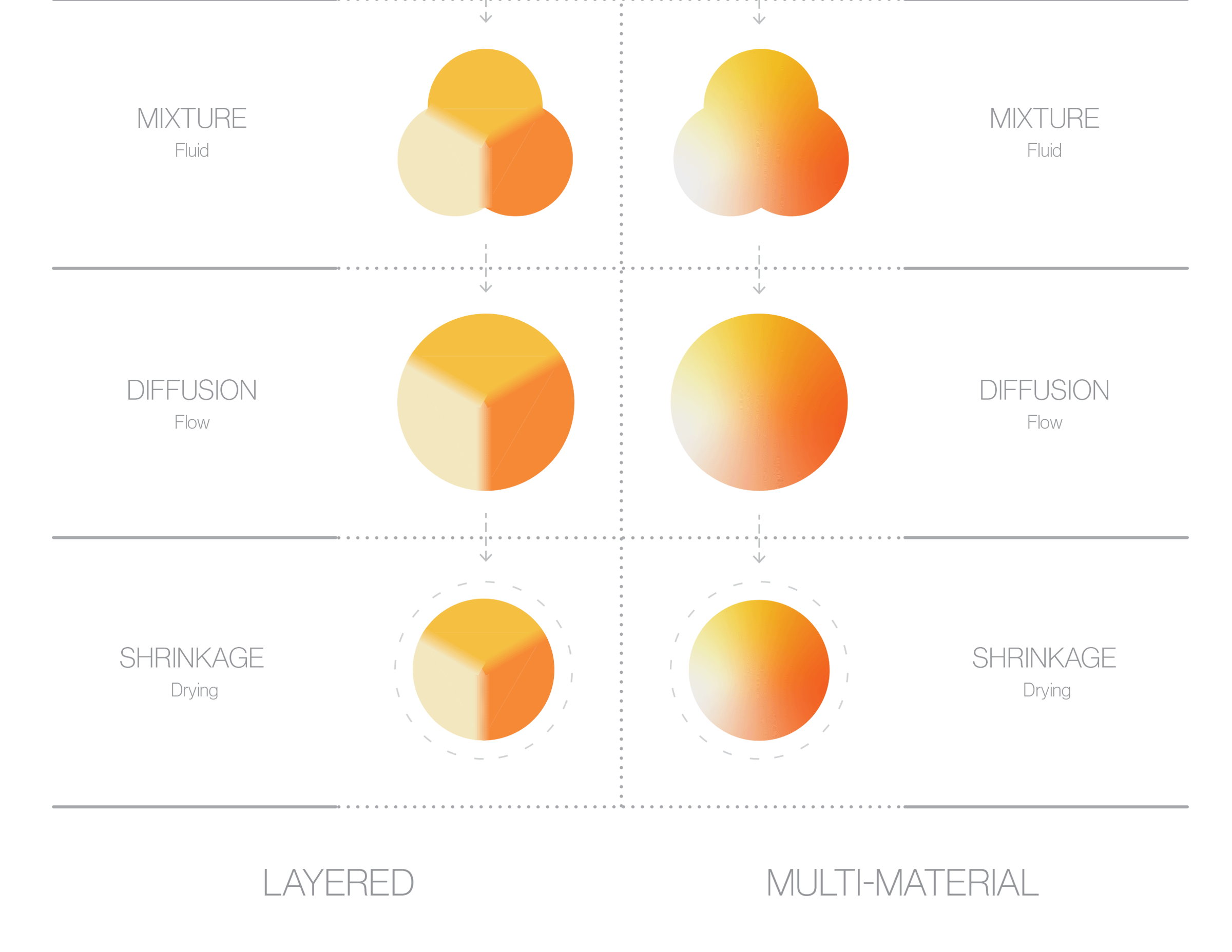
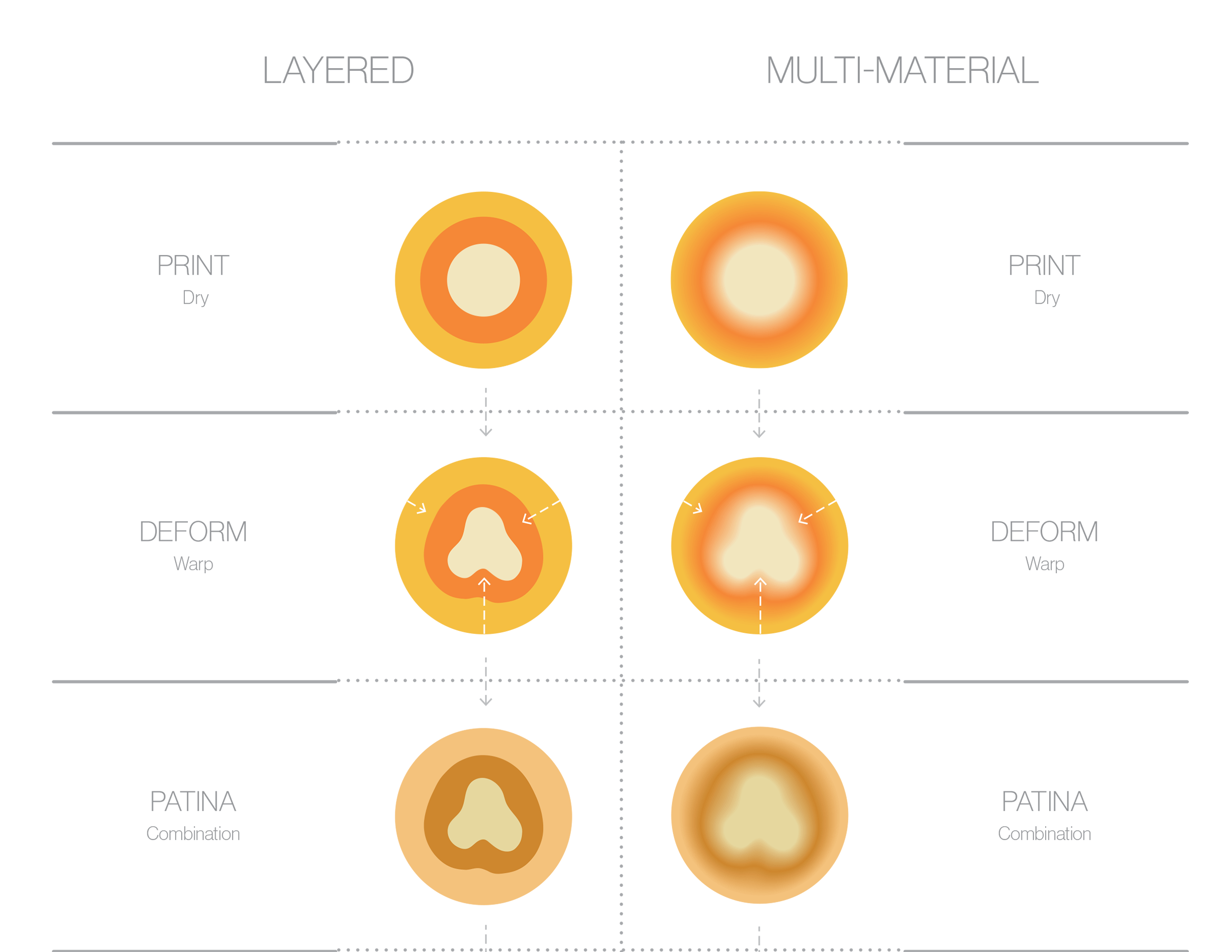
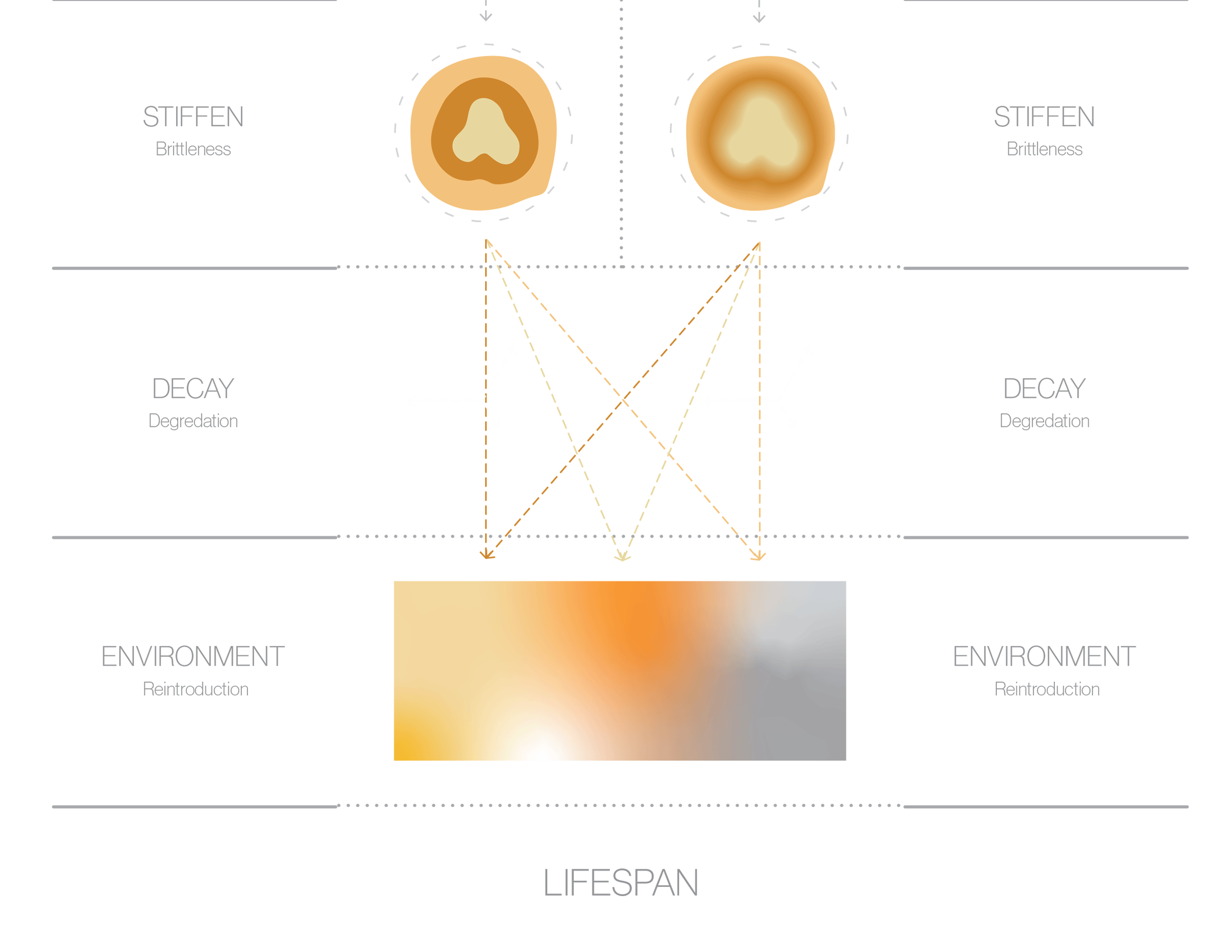
Figure 3:
Diagram showing fabrication processes using layered vs. multi-material hydrogel 3D printing methods.
Figure 4: Diagram showing the general visual and structural changes of layered and multi-material biopolyme prints caused by drying, warping, tinting and stiffening over time.
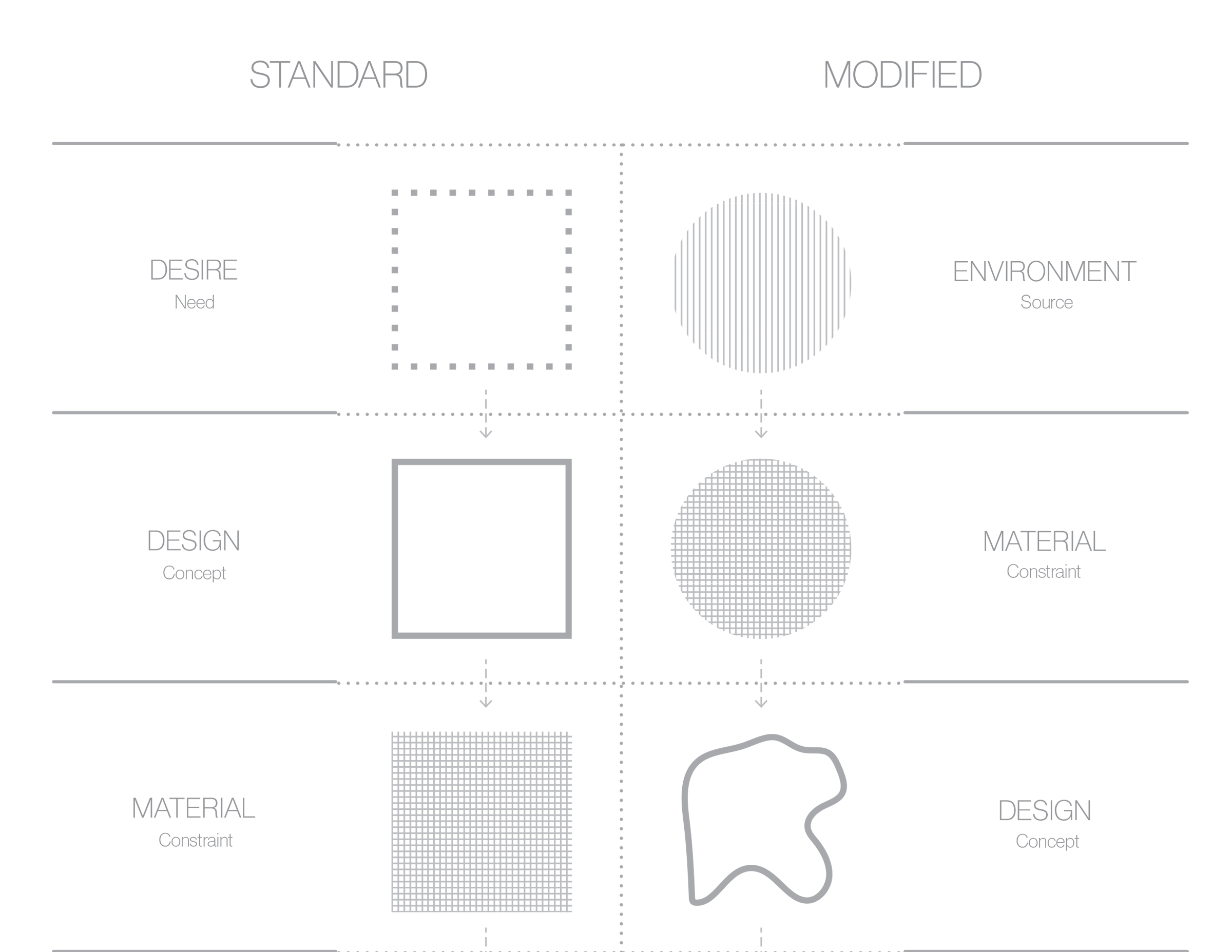
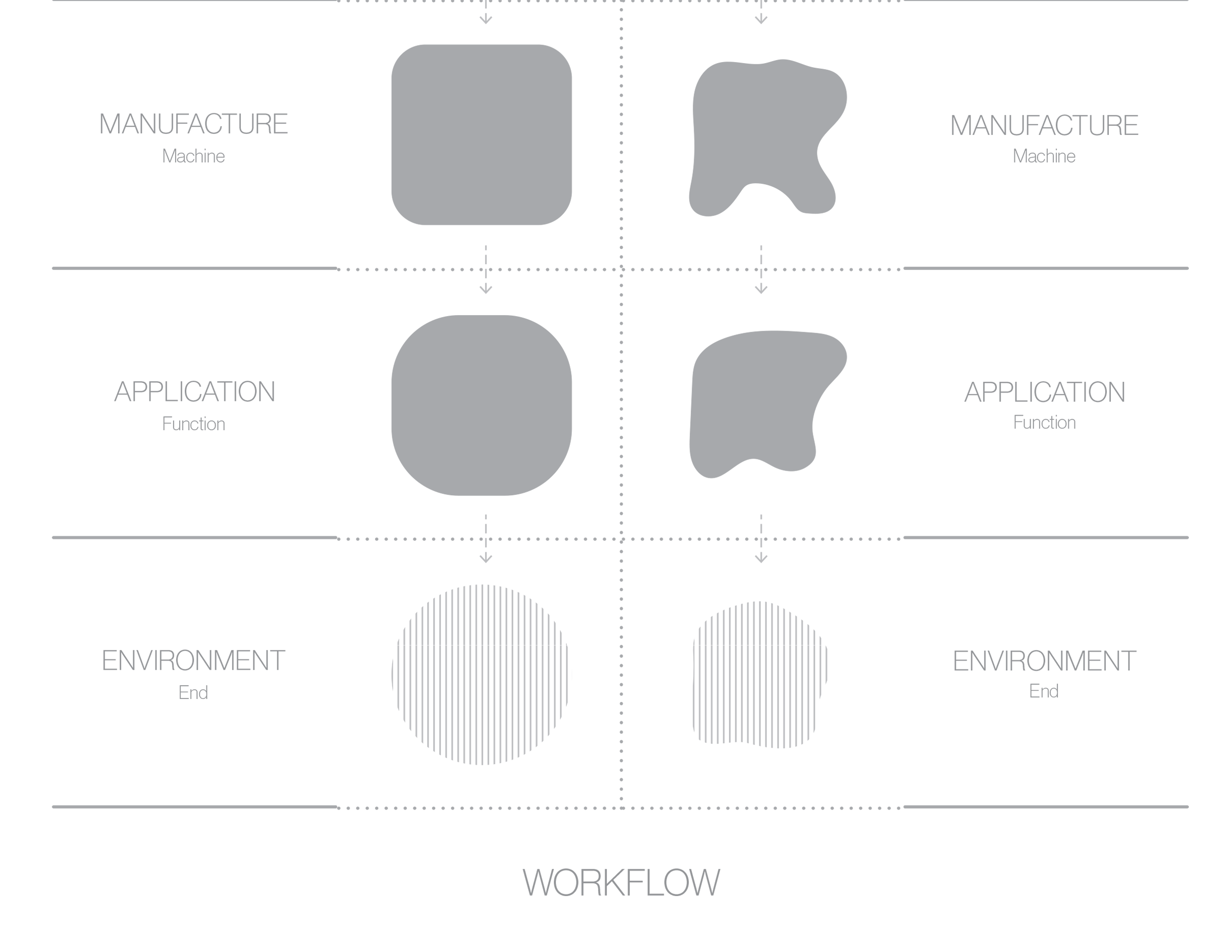
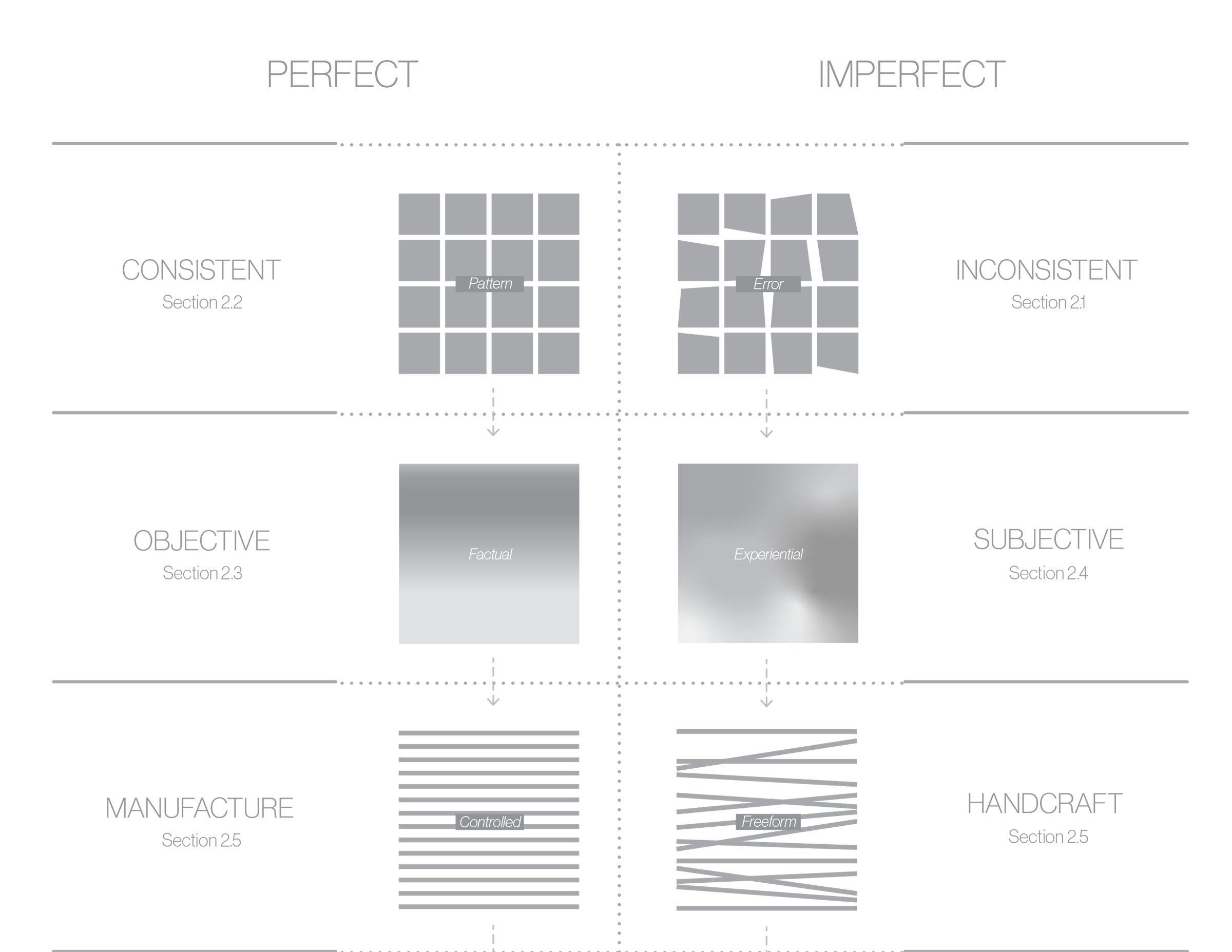
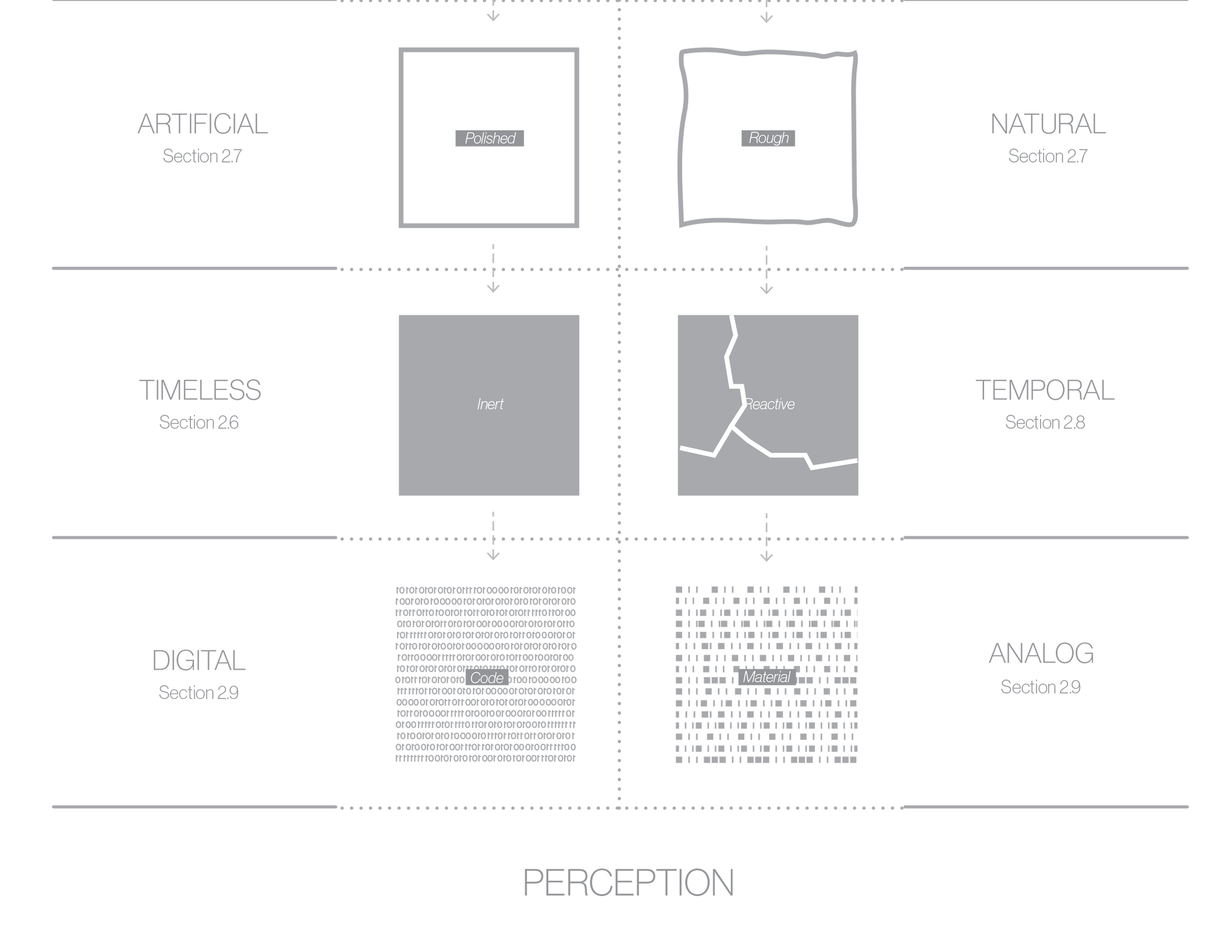
Figure 5: Diagram comparing standard workflows that use inert synthetic materials that prioritize consistency with environmentally aware workflows that use reactive organic materials that accommodate inconsistency.
Figure 6: Content map comparing characteristics associated with the perception of perfect vs. imperfect materials.
+
Process
The unpredictable behavior of products made from reactive materials can present a variety of performative challenges. In particular, the temperature and moisture sensitive properties of biopolymer hydrogels produce a high amount of uncertainty within multiple stages of the manufacturing process. In order to both compensate for and leverage the reactive qualities of these water-based organic materials, we've built a custom biopolymer 3D printer that integrates a digital fabrication workflow with physical material tunability to create objects that can functionalize natural behavioral indeterminacy.
To control unpredictable material behavior, we have established various design and fabrication protocols in order to manage undesirable material uncertainty while encouraging productive material indeterminacy. Although the degradation of the biopolymers is inevitable, the measures seek to limit the circumstances in which the prints will prematurely ferment, lose shape, disintegrate, crack, or warp. This is achieved by controlling for printing parameters such as the extrusion speed, extrusion pressure, nozzle diameter and nozzle height as well as environmental factors such as the material of the print bed or the temperature and humidity of the print room.
At the same time, these procedures are flexible enough to allow for continued experimentation and are not intended to fully constrain the reactive qualities of the water-based materials. The fact that the printed biopolymer skins can change and react over time is a desirable feature of the material that has a practical potential and aesthetic appeal. The biggest challenge of working with biopolymers is finding the ideal balance between control and uncertainty.
To control unpredictable material behavior, we have established various design and fabrication protocols in order to manage undesirable material uncertainty while encouraging productive material indeterminacy. Although the degradation of the biopolymers is inevitable, the measures seek to limit the circumstances in which the prints will prematurely ferment, lose shape, disintegrate, crack, or warp. This is achieved by controlling for printing parameters such as the extrusion speed, extrusion pressure, nozzle diameter and nozzle height as well as environmental factors such as the material of the print bed or the temperature and humidity of the print room.
At the same time, these procedures are flexible enough to allow for continued experimentation and are not intended to fully constrain the reactive qualities of the water-based materials. The fact that the printed biopolymer skins can change and react over time is a desirable feature of the material that has a practical potential and aesthetic appeal. The biggest challenge of working with biopolymers is finding the ideal balance between control and uncertainty.