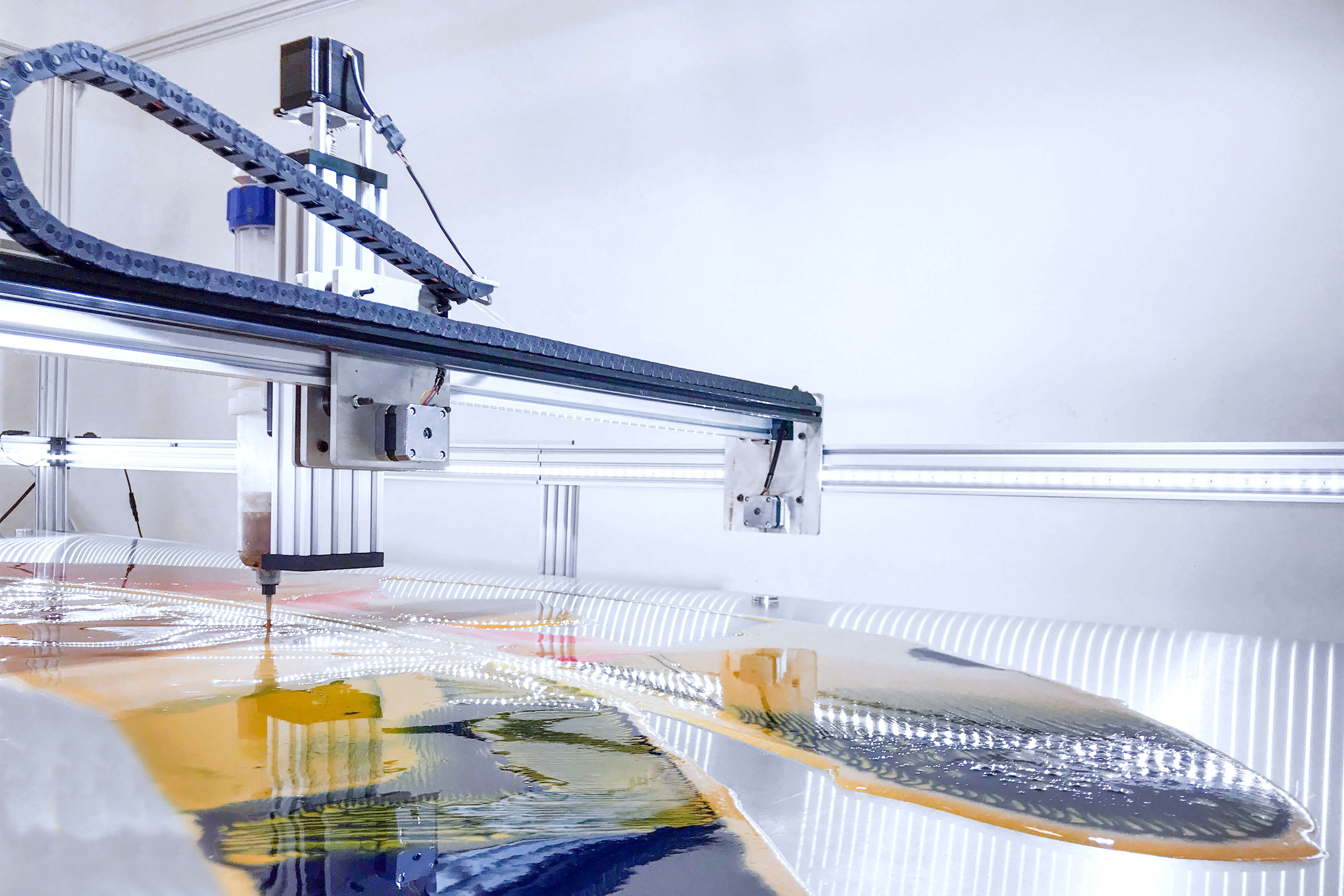
Figure I: Biopolymer printing gantry photo with pneumatic extruding end effector depositing different liquid hydrogel onto print bed.
Figure II: Biopolymer printing gantry photo with perspective elevation drawing showing set up in print room with end effector, print bed, drying beds and integrated lighting for imaging and recording experiments.

Figure III: Series of 360 ml cartridges containing colored pectin hydrogel. (left to right) Black – Charcoal, Dark Blue – Indigo, Dark Green – Spirulina, Green – Matcha, Yellow – Turmeric, Dark Red – Beet, Dark Brown – Cinnamon, Brown – Pomegranate, Light Orange – Chitosan, Orange – Standard, Light Tan – Calcium.



Figure IV: Technical isometric drawing of the CNC biopolymer printing gantry showing print and drying beds with detail drawing of the end effector with removable cartridges and nozzles diameters.
+
Printer
Mediated Matter Group, MIT Media Lab
A custom made 3 Axis CNC gantry controls the position of the print head over a 4’x 8’ printing surface. The X and Y-axis of the machine are actuated by two pairs of NEMA 17 stepper motors that move along aluminum extrusion rails connected to timing belts. The Z-axis is controlled by a linear actuator that moves the print head with a worm screw. A fixed cartridge container with an airtight connector allows users to swap out cartridges easily. The entire printing assembly cost about $6,000.
The end effector consists of a pneumatic system with a pressure regulator that pushes a piston into a cartridge to extrude material through a tip adaptor attached to a nozzle of varying diameters. The size of the nozzle will control the width and precision of the extruded material on the toolpath. A thinner nozzle will extrude less material at a time to allow for higher degrees of precision. In comparison, a wider nozzle will extrude more material to allow for more efficient print times.
For purposes of consistency, we have chosen to use a 16-gauge diameter nozzle that allows a balance between precision and efficiency. The pressure and speed can be predefined or overridden mid-print to deposit more or less hydrogels on the printbed. The printer is programmed to cut off the pressure and lift the nozzle as it moves between the start and endpoints of consecutive toolpaths. The nozzle height and diameter determine the precision of the biopolymer prints. Typically, the nozzle is 2-6 mm from the printing surface to ensure that the materials are being precisely extruded to the correct regions. If the nozzle is much farther away than 5mm, the hydrogels will extrude with slight inconsistencies that will cause coiling.
A custom made 3 Axis CNC gantry controls the position of the print head over a 4’x 8’ printing surface. The X and Y-axis of the machine are actuated by two pairs of NEMA 17 stepper motors that move along aluminum extrusion rails connected to timing belts. The Z-axis is controlled by a linear actuator that moves the print head with a worm screw. A fixed cartridge container with an airtight connector allows users to swap out cartridges easily. The entire printing assembly cost about $6,000.
The end effector consists of a pneumatic system with a pressure regulator that pushes a piston into a cartridge to extrude material through a tip adaptor attached to a nozzle of varying diameters. The size of the nozzle will control the width and precision of the extruded material on the toolpath. A thinner nozzle will extrude less material at a time to allow for higher degrees of precision. In comparison, a wider nozzle will extrude more material to allow for more efficient print times.
For purposes of consistency, we have chosen to use a 16-gauge diameter nozzle that allows a balance between precision and efficiency. The pressure and speed can be predefined or overridden mid-print to deposit more or less hydrogels on the printbed. The printer is programmed to cut off the pressure and lift the nozzle as it moves between the start and endpoints of consecutive toolpaths. The nozzle height and diameter determine the precision of the biopolymer prints. Typically, the nozzle is 2-6 mm from the printing surface to ensure that the materials are being precisely extruded to the correct regions. If the nozzle is much farther away than 5mm, the hydrogels will extrude with slight inconsistencies that will cause coiling.